Fault Diagnosis Of Cummins 300KVA Generator Fuel Supply System
- Admin
- May 14, 2022
- 4 min read
1.Fault diagnosis of high pressure common rail fuel supply system of 300kva Cummins diesel generator set.
The sensors and actuators used in the high-pressure common rail fuel supply system have the characteristics of large number, high precision and fast feedback. As long as one element is damaged, it will have a great impact on the whole system, and even lead to the failure of normal operation or start-up of the equipment. The problems faced by the fault diagnosis of the system are also the most critical.
Because the structure and control mode of the high-pressure common rail fuel supply system are very different from the traditional diesel generator, the faults in the system are also more complex. Generally, the faults can be divided into the following types.
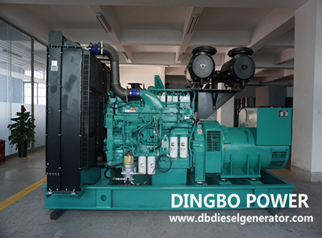
(1) Fuel supply system failure caused by low pressure part.
① There is a problem with the fuel transfer pump. The fault phenomenon is that the engine stalls after warming up, the idle speed is unstable and the acceleration is weak. You can connect the oil pressure gauge in series between the oil tank and the oil circuit of the primary fuel filter, check the oil pressure value (the oil pressure should be greater than 3bar during rapid acceleration), judge the condition of the fuel transfer pump, and eliminate the fault by repairing or replacing the fuel transfer pump.
② The problem of fuel filter shows that it is difficult to start cold, which is mainly caused by too much water in the filter or damage to the heater, especially in winter. In winter, the water in the filter of 300kva Cummins diesel generator should be discharged regularly and the working condition of the heater should be checked.
(2) Fuel supply system failure caused by high pressure part.
The high-pressure part of the fuel supply system uses the cam to drive the pump plunger of the high-pressure pump up and down to complete the oil suction and pumping process.
① There is a problem with the high-pressure pump. The fault phenomenon is that the high-pressure pipeline has insufficient fuel pressure due to the damage of components in the high-pressure pump. The fault of the high-pressure pump can be judged by reading the fault code of the common rail pressure sensor and data flow analysis.
② There is a problem with the common rail pressure sensor. The fault phenomenon is that the engine stalls after starting, and cannot be started again after stalling. The reason is that the oil measuring hole of the common rail pressure sensor is blocked or the sensor is damaged, resulting in abnormal signal of the common rail pressure sensor detected by ECU, forcing the engine to shut down. Use a multimeter or oscilloscope to detect the output voltage signal of the sensor (the normal value is 0.5 ~ 4.5V), so as to judge this kind of fault.
③ There is a problem with the common rail pressure limiting valve. The fault phenomenon is difficult to start, unstable idle speed and weak acceleration during driving. The reason is that the fuel pressure in the common rail is large and insufficient due to the leakage of the common rail pressure limiting valve. It can be judged by analyzing the data flow of common rail pressure sensor with detector or oscilloscope under the condition of landing.
④ There is a problem with the electronic fuel injector. The fault phenomenon is that it is difficult to start the hot vehicle and black smoke is emitted from the exhaust pipe. The reason is that the mixture is too rich due to poor injection or oil dripping of the electronic fuel injector. Check and analyze the current waveform of fuel injector with oscilloscope or tester to further judge the fault of fuel injector and replace it.
3. Misunderstanding of fault diagnosis and maintenance.
In the process of fault detection and judgment of high-voltage common rail system of electronically controlled diesel generator, it is a more direct method to directly read the fault code with computer detector to diagnose the fault. Therefore, many maintenance personnel directly use the read fault code to judge the fault location, or try to eliminate the fault by replacing the components and parts displayed by the fault code, However, the fault can not be eliminated, because the fault code does not mean that the components referred to in the fault code really have a fault. This is because the fault conditions and thresholds set by ECU for each component are different, and the interaction between various components and other factors exist. Some of the fault codes stored by ECU can reflect the real situation of the fault, while others cannot. For example, some faults are caused by mechanical faults, which make the signal of the sensor deviate or exceed the range, and the ECU will report the sensor fault. In fact, the sensor is not the fault point.
In short, a fault code does not mean that there must be a fault, and no fault code does not mean that there must be no fault. Diagnosing the fault location through the fault code can only be used as a reference. It also requires the maintenance personnel to determine the key inspection objects after careful analysis and judgment according to the accumulated experience, knowledge and technology. With the help of instruments and meters to detect the performance parameters of components, we can judge the authenticity of fault code, find out the real cause of fault and determine the fault location.
Comments